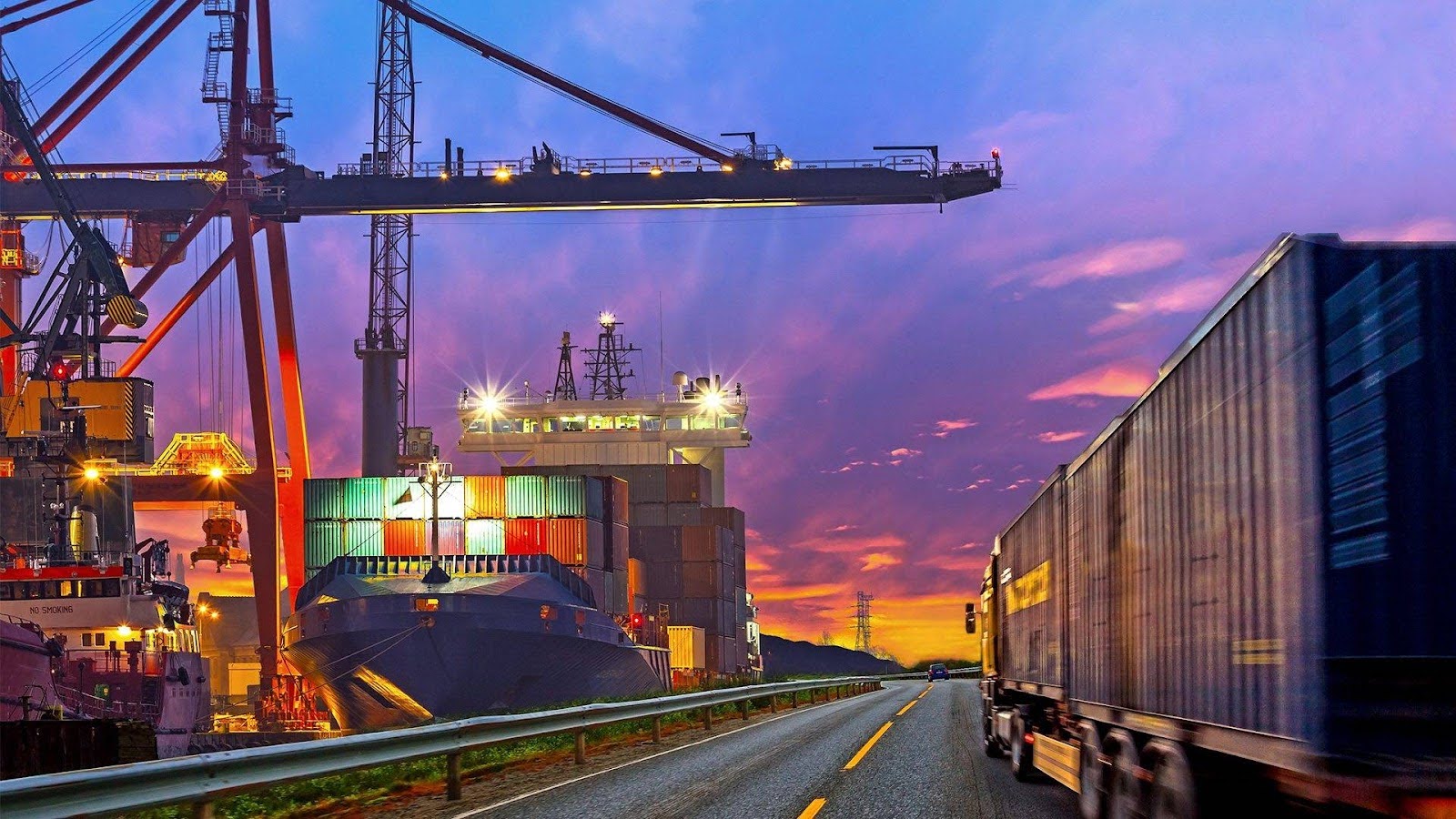
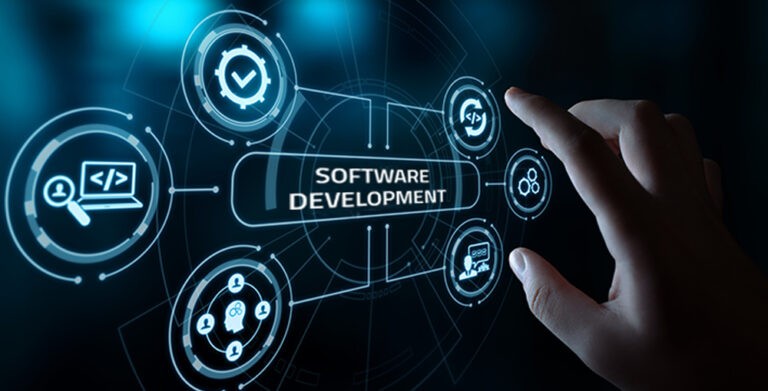
Logistics
Queue Management
The logistics industry faces a silent yet significant problem: queuing and the mismanagement of waiting times. Picture this: a truck arrives at a distribution center, only to be met with long lines and excessive waiting—an all-too-familiar scenario for logistics managers around the globe. This inefficiency does not merely lead to frustration; it translates to increased operational costs, delayed shipments, and ultimately dissatisfied clients. In an industry where time is money, the repercussions of poor queue management can be devastating.
The reality is, many logistics companies still rely on outdated methods to manage their queues. Paper-based systems, rudimentary scheduling, and a lack of real-time data can exacerbate delays, making it imperative for organizations to recognize the gravity of the situation. In this blog, we will dive deep into the pain points of logistics queue management and explore strategic solutions that can help streamline operations.
A primary driver of inefficiency in logistics is the inability to predict and manage queuing effectively. A myriad of challenges contributes to this issue, including:
- Unpredictable Arrival Patterns: Freight deliveries do not always conform to a set schedule. Unexpected surges in delivery volumes can lead to congested terminals, where vehicles are left idling for hours. This unpredictability disrupts not just the specific logistics provider but also their clients, and the ripple effects can be felt throughout the supply chain.
- Inefficient Resource Allocation: Without a robust queue management system, resources such as loading docks, personnel, and equipment often sit idle or are misallocated. When queuing isn’t properly managed, it leads to additional costs as companies may need to bring in extra labor or equipment to cope with demand spikes.
- Customer Satisfaction Risks: Slow service and long waiting times threaten customer satisfaction. Today’s consumers expect timely deliveries and efficient handling of goods. Failing to meet these expectations can lead to the loss of business and a damaged reputation.
- Data Silos: Many logistics providers utilize fragmented systems for tracking and managing queues. Without a comprehensive data management approach, teams may struggle to identify bottlenecks or assess performance metrics, further complicating the queuing issue.
Here’s how logistics companies can turn around their queuing challenges:
- Adopt Advanced Queue Management Systems: Implementing a dedicated queue management solution can dramatically enhance operational efficiency. Such platforms offer real-time data on truck arrivals and wait times, empowering logistics managers to make informed decisions and allocate resources accordingly.
- Utilize Predictive Analytics: Leveraging predictive analytics can help companies anticipate peak times and plan resources proactively. By analyzing historical data, logistics managers can forecast traffic patterns and optimize scheduling, thus reducing congestion and minimizing idle times.
- Enhance Communication Channels: Establishing solid communication frameworks between stakeholders is crucial. Using mobile apps or real-time communication tools can ensure that drivers are updated about their status, instantaneously notifying them of any delays or changes in scheduling.
- Incorporate RFID and IoT Technologies: The implementation of RFID tags and IoT devices can significantly streamline the loading and unloading processes. With accurate tracking of goods, logistics operators can enhance inventory control and ensure that items are moved freely through the system, minimizing queues at loading docks.
- Continuous Training and Development: The human element cannot be overlooked in queue management. Regular training sessions for staff on the latest technologies and processes can empower them to find inventive solutions to queuing challenges. By fostering a culture of continuous improvement, organizations can adapt more readily to unforeseen demand fluctuations.
- Establish Flexible Dock Scheduling: Creating a flexible scheduling system could alleviate peak-time pressures. By allowing carriers to book appointments in advance, logistics providers can better manage their workloads, smoothing out demand fluctuations.
The burden of managing logistics queues is a pain point that many in the industry feel acutely. If you find yourself grappling with inefficiencies, it’s crucial to take immediate steps to enhance your queue management strategies. Implementing advanced technology solutions and focusing on improved communication will yield dividends in efficiency and customer satisfaction.
In conclusion, the challenges posed by queuing in logistics should not be underestimated. By recognizing the issues and adopting innovative and effective solutions, companies can dramatically enhance their operational efficiency, reduce delays, and ultimately improve customer satisfaction. The path to smoother logistics is clear—embrace the change before it’s too late.
Related Blogs
Customer Experience in Banking
Looking to improve customer experience in banking? Find out how CJM tools enable personalization at scale and drive deeper customer relationships.
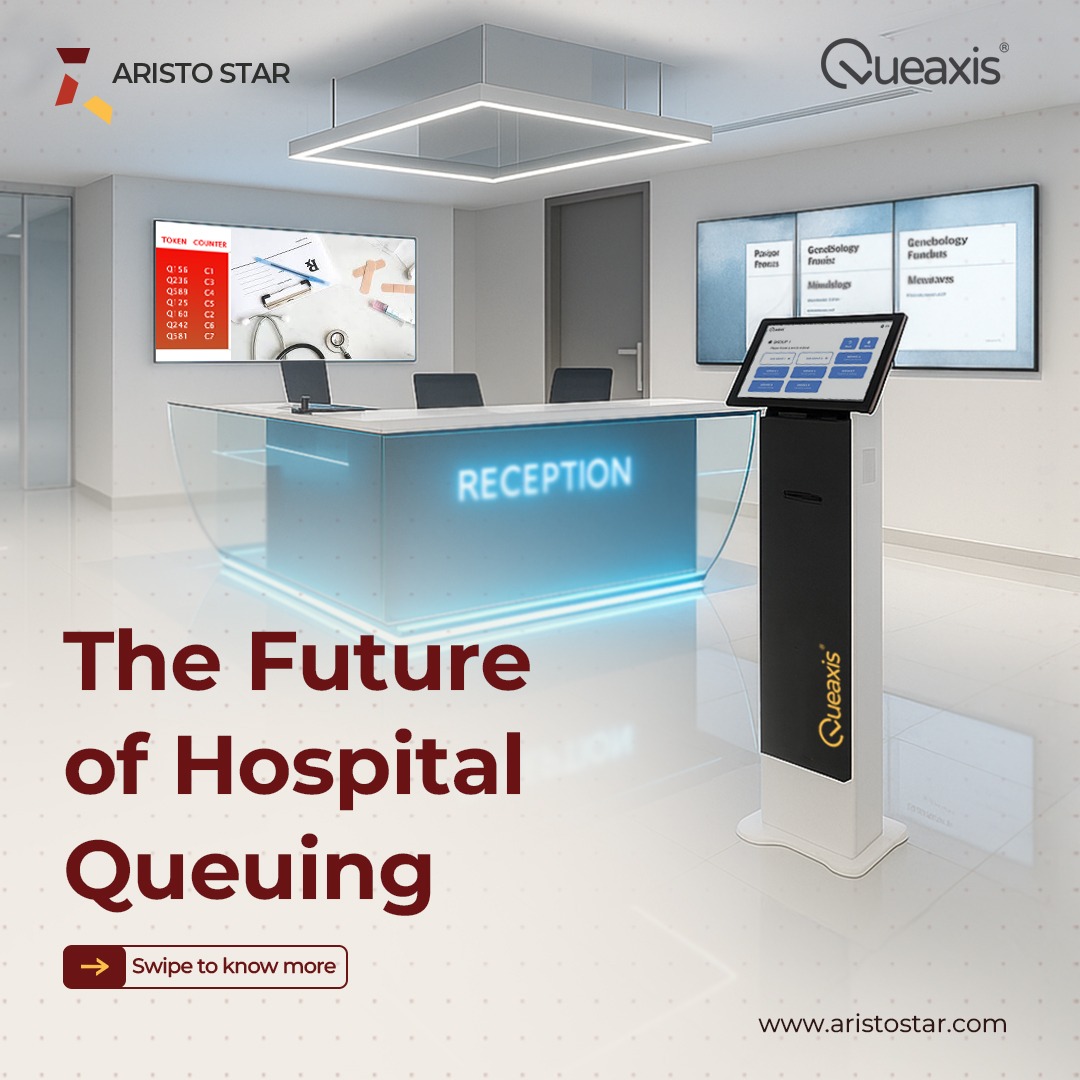
Patient Journey Mapping to Improve Hospital Experience
Every hospital visit is more than a medical procedure; it's a personal story filled with emotions, expectations, and interactions.
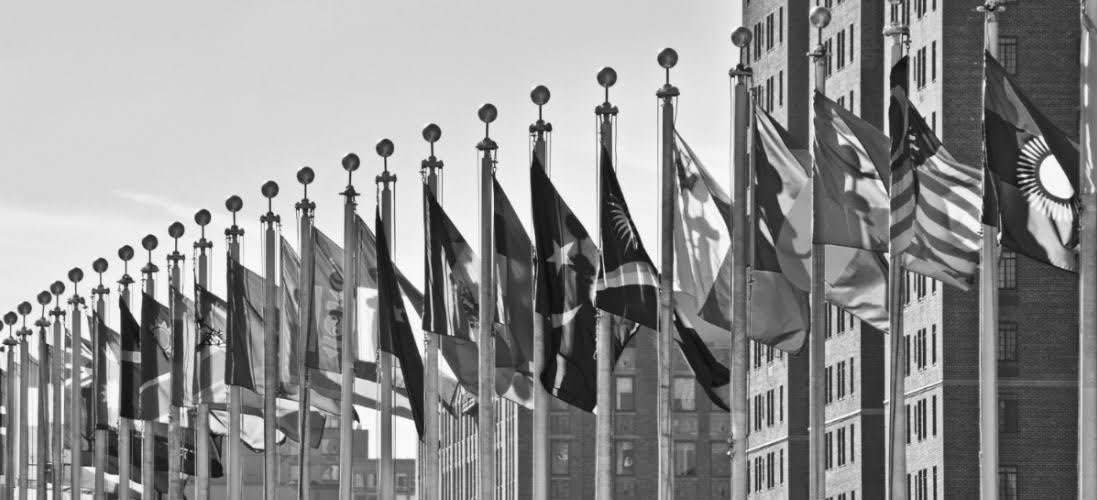
Government
In today’s fast world, government entities are increasingly challenged to deliver services efficiently while ensuring public satisfaction.